For this week’s edition of the Northern Heat Report, we thought we’d switch things up a bit. We wanted to hear from a luthier who has used our Obsidian Ebony. This gives us and other instrument makers a deeper insight into the technical aspects of working with this ebony alternative.
The luthier we spoke to was Geoffrey St Germaine of St Germaine guitars out of Halifax, Nova Scotia, Canada. Geoffrey is a talented luthier, who has built many beautiful instruments, which you can see on his Instagram page here: St Germaine Guitars
Here are the questions we asked, and the answers provided. We want to thank Geoffrey for participating in this Q&A and for providing valuable information.
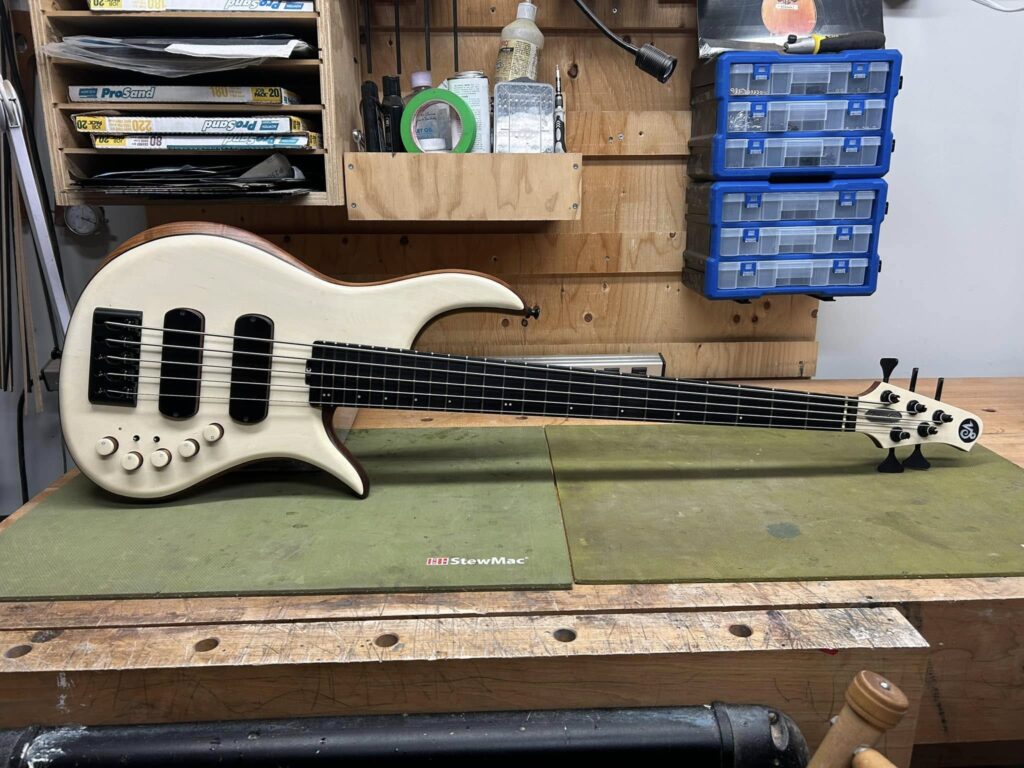
- What projects did you create using Obsidian Ebony?
I have used Obsidian Ebony to create fretboards and other trim for my bass guitars.
- What drew you to use Obsidian Ebony for these particular projects?
I have been using a number of Ebony substitutes over the past 5-6 years to address dwindling supplies, rising prices and lowering qualify of available Ebony (Diospyros crassiflora). I have also been pursuing a shift to using more domestic woods in my instruments in order to use material that is produced using sustainable practices. This has led me to a few different products such as Rocklite, Royal Blackwood and Richlite.
As Thermalwood is a Canadian company, I was quite intrigued once I learned of their Obsidian Ebony product. I have subsequently used Obsidian Ebony on six bass guitars and have found it to be superior to the other products I have used both in workability and final appearance. Unlike some other products, the finished product does not project a blue tint, which seems common in some of the other dyed products. It very much presents with a brown tint, which I find gives it a more natural appearance. I will admit that the appearance of blue-coloured dust while sanding it did concern me, but this doesn’t show in the finished product.
- How was your first impression of the material when you started working with it?
My first impression with the material was very good. In creating a fretboard, I use a number of tools including a thin-kerf saw mounted in a table saw to cut fret slots, bandsaw to cut the material to rough final size, routers with template bits to get to final size, hand planes to rough in surface radius and curved and flat sanding blocks to achieve the final fretboard surface that is suitable for fret installation. With all of these tools, Obsidian Ebony performed very well and much like normal wood, it has its strengths and weaknesses in each of these areas.
- How did Obsidian Ebony respond to cutting, shaping, or carving tools?
In general Obsidian Ebony performed quite similarly to hard Maple for cutting, shaping and carving. I have found it a little more prone to tear out with router bits, but not dissimilar from any roasted/torrefied Maples. Compared to Gaboon Ebony, it responded much more favourably, particularly to router bits and to hand planes. I cannot rough in fretboard radii with a handplane when working with Gaboon Ebony as there is commonly interlocked grain areas that produce substantially tear out even with a freshly sharpened blade.
- Was the material easy to sand, polish, or finish?
Obsidian Ebony was a joy to sand, polish and finish. Sanded to P400 for fretboards with Osmo PolyX oil produced a fantastic satin fretboard appearance that was fast and simple to achieve.
- What do you think about the appearance of Obsidian Ebony in the finished product?
It’s fantastic! It is properly black with a brown tint to replicate the appearance of Gaboon Ebony. Further, the grain of the Maple is still visible in the fretboard giving it a more natural appearance when viewed up close. Some of the other ebony replacements have an extremely uniform and unnatural appearance. That said, I would be very curious to see this process applied to exceptionally flamed Maple.
- What advice would you give to someone working with Obsidian Ebony for the first time?
Pay attention to grain direction and move slowly when routing. Other than that, it can be treated the same as a conventional hardwood.
- Is there anything unique about Obsidian Ebony that you haven’t experienced with other materials?
Compared with other replacements, it does have a similar odor to other hybrid/composite type products, that is a distinctly chemical smell. In terms of workability, it is nothing outside the norm of working a different species of wood.
- If you could improve one aspect of the material, what would it be?
I would say the smell, however, I expect this is related to a resin or dye that has been selected based on performance and I would not want to address this issue if it meant compromising the performance of the product.